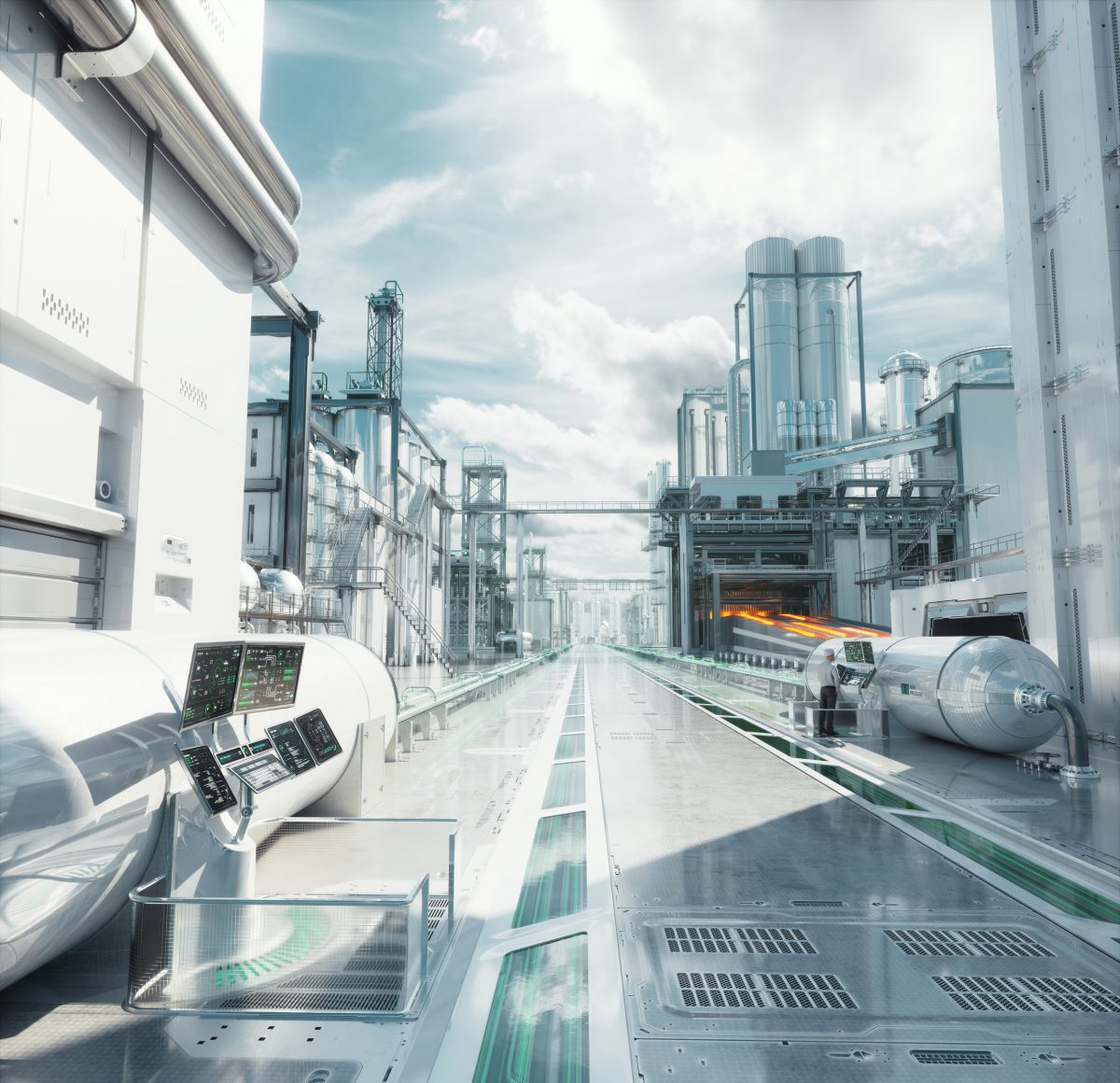
From assembly robots to automated warehouses – artificial intelligence (AI) and the manufacturing industry are a match made in heaven. And this just the beginning. According to a report by IDC, by 2021, 20 percent of leading manufacturers will rely on embedded intelligence (using AI, internet of things and blockchain applications) to automate processes and speed up execution times by up to 25 percent.
How is AI improving the bottom line?
Microsoft’s recent research explains how that’s benefitting firms: manufacturing businesses in the US using AI are performing 11.5 percent better than those that aren’t. AI benefits industry. Why? Its possible applications are extensive. And the stats are enticing. According to McKinsey, 50 percent of companies that invest in AI over the next five to seven years will have the potential to double their cash flow; manufacturing is leading the way due to its heavy reliance on data.
In a recent Forbes insight survey on AI, 44 percent of respondents from automotive and manufacturing think AI will be important to manufacturing in the next five years, while almost half (49 percent) said it was critical to success. From real-equipment maintenance to more streamlined design processes, let’s take a look at some AI-led trends.
The age of human-robot collaboration
Poor maintenance can reduce a manufacturing plant’s overall productive capacity by as much as 20 percent. No wonder then, that industrial robots with embedded AI are proving popular will manufacturers.
KUKA, the Chinese-owned German manufacturing company, is one of the largest manufacturers of industrial robots in the world, and they’re making slick new movements. KUKA claims their LBR iiwa “is the world’s first series-produced sensitive robot,” which “signals the beginning of a new era in industrial robotics, where humans and robots can work side by side in close co-operation.”
No threat of robots outmoding us then, they claim. And it’s working. LBR iiwa units are used at the BMW Group Plant in Munich, Germany, where they’re helping workers insert components into car bodies during construction.
Next-generation software design
It’s a new way of looking at things: designers or engineers enter their ultimate design goal into generative design software, complete with cost constraints, preferred materials and methods. The software then takes the original idea and explores different solutions to make it a reality on the spot. The result: you get many design possibilities, a conclusion of whether they’ll work or not, and a recommendation for the best solution. It could be used from everything from aircraft wing design to plastic molds for a phone case. Brian Matthews, Vice President of Platform Engineering at Autodesk, US, says it could achieve 50,000 days of engineering in one day.
Connecting the dots with smart manufacturing
Put simply, smart manufacturing is the use of industrial IoT devices – those connected through the internet, able to send and receive data – and AI. According to a report by TrendForce, smart manufacturing could be worth over $320bn in 2020. And some of the big players in the industry are already well ahead in this trend.
Siemens launched Mindsphere in 2016, its smart cloud for industry, allowing manufacturers to monitor machinery. For example, its latest gas turbines, packed with over 500 sensors that monitor their condition from temperature to pressure, allowing for real-time updates when they need repairing.
General Electric has a similar idea with their Brilliant Factories, which utilize AI tracking and processing in the manufacturing process to find issues as they emerge. These factories are powered by Predix, their industrial IoT platform; it uses sensors to automatically capture every step of the process and monitor each piece of equipment. And the results speak for themselves. 18 percent improved equipment effectiveness at a factory in Pune, India, and a 25 percent increase in on-time delivery rates at a jet engine factory in Muskegon, US.
Predictive maintenance becoming part of the program
Predictive maintenance. In short: manufacturing machines repairing themselves, without our help. One step towards the era of robots? Perhaps. A load off the factory manager’s mind? Definitely. IoT sensors and advanced analytics make it so, and it’s set to save businesses heaps of time and resources.
It’s already in action. A report by Deloitte explains how predictive maintenance is built into machines used for manufacturing titanium implants. Let’s break it down: titanium is so strong that it requires tools with diamond tips to cut into it, but often these tips become dull from overuse. In comes predictive maintenance, which uses the sensors and monitors to assess the shape of the machinery. In turn, they can give a warning to engineers when the tips need to be changed.
Eagle-eyed supercomputers
Similarly, as impeccable as our eyes are, they miss things. We’re only human. This is why startups like landing.ai have developed machine-vision tools to find microscopic defects in products like circuit boards. These tools use machine-learning algorithms trained on remarkably small volumes of sample images. They can detect not only minor defects but also send immediate alerts to manufacturers.
Evolution, not revolution
Automation and machine learning have been around in the manufacturing sector for decades, so these developments are an evolution, not a revolution, for the industry. If you’ve not thought about how AI could affect your business or even your competitors, now’s the time to explore it.
Greater industrial connectivity, more sensors, powerful analytics and robots (to name a few) bring distinct challenges. Aime Lachapelle, of Emerton Data, says that 85 percent of the companies they surveyed aim to implement AI into their production processes. However, less than 30 percent have an AI development plan. While many manufacturers have aspirations to implement AI into operations, thorough research and training are needed beforehand.
It’s time to optimize your cybersecurity
These technologies have the power to change the manufacturing industry for the better. But with new technology comes new risks. Anton Shipulin comments:
Manufacturing companies looking to implement machine learning, automation and general AI into their operations should invest in specialized industrial cybersecurity solutions to protect their innovations. With a better-optimized cybersecurity solution, you vastly reduce the risk of unwanted cyberattacks.
Anton Shipulin
Global Presales Manager, Kaspersky Industrial CyberSecurity