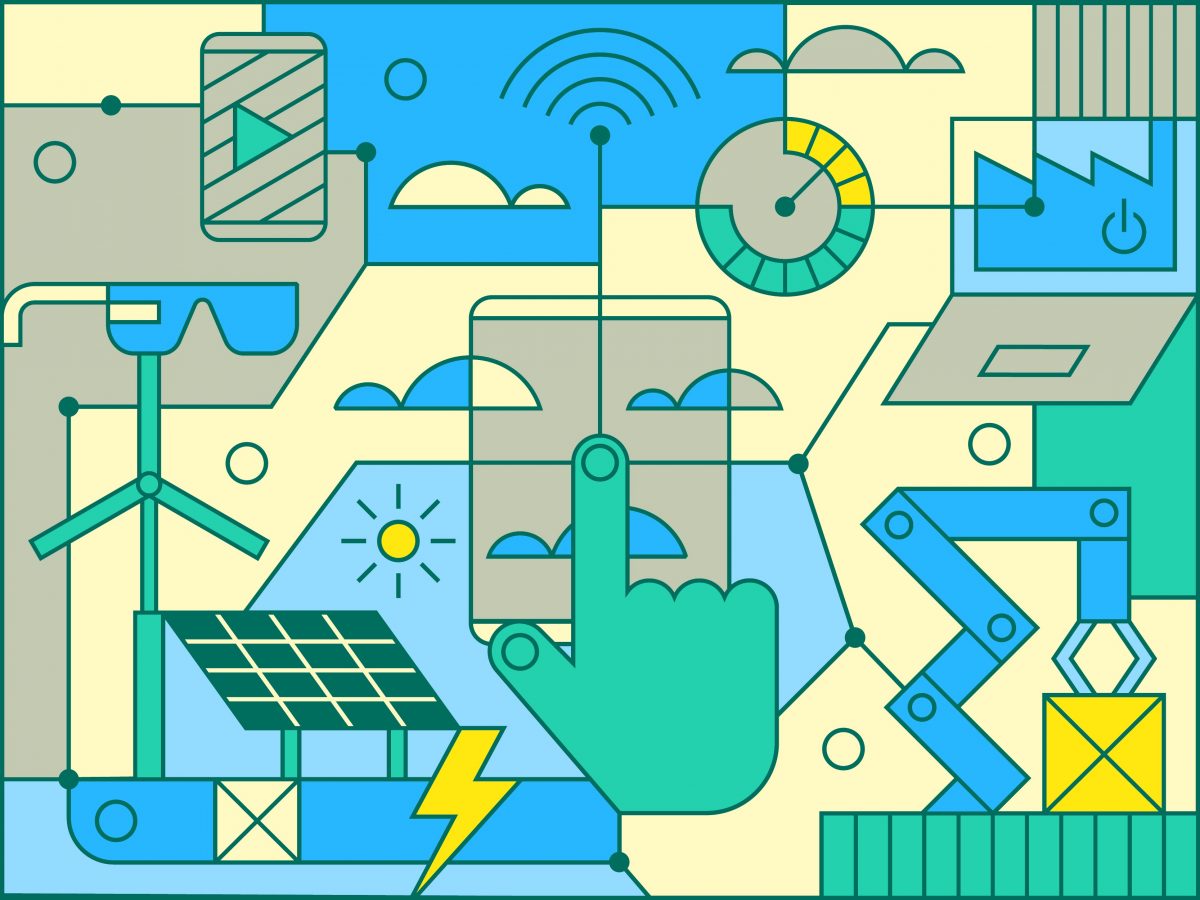
By 2025, there will be over 75 billion internet-connected devices, embedded into objects ranging from smart home thermostats to control systems on factory floors. In the industrial sector alone, the Internet of Things (IoT) is expected to near a trillion dollars in value by 2025. We’re now living in the midst of the fourth industrial revolution, a period of great transformation driven by the rise of smart factories, big data and machine learning. These technologies are forming the foundational infrastructures of our industry today.
The impact of industrial IoT
This connectivity and scalability continue to have a profound impact on our lives. It’s also driving change behind the scenes in the form of industrial smart technology that our infrastructures are growing increasingly reliant on.
This is the dynamic world of the industrial internet of things (IIoT), where cutting-edge solutions like industrial control systems power automation on the factory floor. But the implications of connected technology in the industrial sector can come with a big impact – and equally big responsibilities. These machines could in the future control everything from the delivery of our gas, electricity and water to the manufacture of every individual component that’s inside the devices we use every day.
Airbus – a brief case study
Here’s an example: Airbus, the second-largest aviation and defense contractor in the world, recently launched a digital manufacturing initiative dubbed the ‘Factory of the Future‘. To suggest that building a commercial airliner or spacecraft is a complex affair would be an understatement. Comprising millions of components and many tens of thousands of assembly steps, there are many things that can go wrong during the manufacturing process and a mistake can be catastrophic to passenger safety. To mitigate these risks, Airbus is integrating sensors in its machines to carry out proactive maintenance. This lets maintenance teams carry out proactive repairs before a dangerous (and very costly) problem occurs that could lead to a major disruption of operations. Predictive maintenance should combine IIoT sensors with secure data communication protocols, root cause analytics and centralized or distributed data storage to create a more streamlined environment that provides real-time insights into reducing downtime and investigates events before they become problems.
Enhancing quality with data-driven decisions
Information silos, in which different departments don’t collaborate and communicate efficiently, have long plagued enterprise environments. Many established industrial-sector enterprises, despite having plenty of funding, still run on outdated systems and processes in which there’s a major disconnect between, for example, people working on the production floor and those in back-office roles. This lack of a consolidated ecosystem leads to miscommunications, and all the reduced efficiencies and compromises on quality that come with it. By building a single, cohesive environment that combines aggregated product data with insights from workers in the production facility, executives can make more informed decisions that improve everything from product quality to worker safety. Some enterprises create so-called digital twins to build enhanced testing environments to demonstrate the risks and opportunities of prototypes in development.
How to keep the industrial internet of things secure
While technological innovation is transforming the industrial sector beyond measure, it comes with significant risks that need to be mitigated from the outset. Just like any other connected technology, industrial control systems on production floors can be attacked by cybercriminals. Given that some industrial systems power critical infrastructure, the stakes can be high, so it’s important to continually invest in testing to expose potential vulnerabilities. For example, Kaspersky published research exploring vulnerabilities in UPC Unified Architecture (UPC UA) protocol.
To avoid these risks, industrial operations need to modernize with a security-first approach that lets them innovate without leaving themselves exposed to today’s many cyberthreats.